4 ways SmartMore machine vision can help ensure food safety

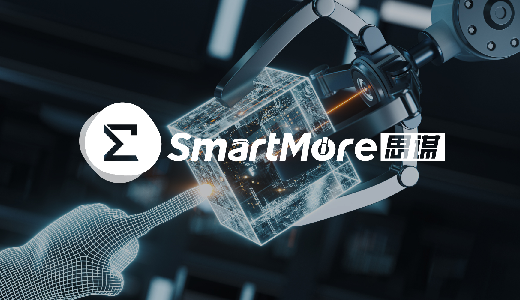
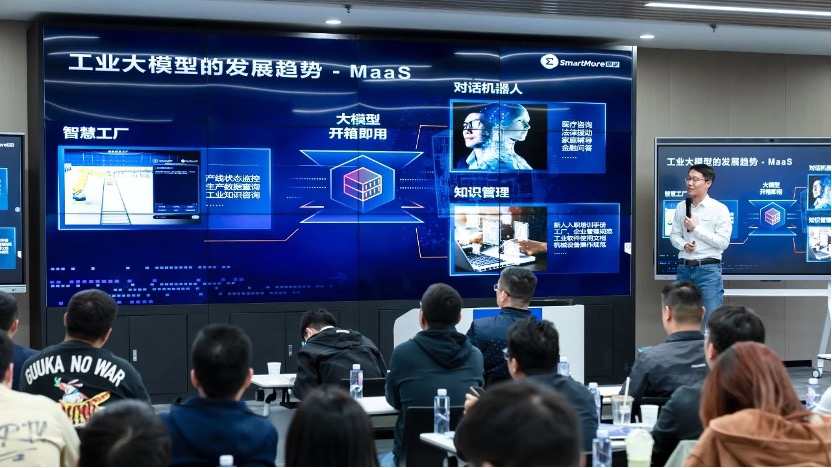
Food safety is a critical concern for both consumers and food manufacturers. As the World Health Organization (WHO) indicates, about 600 million people worldwide become ill due to contaminated food every year, and 420,000 die as a result. In the United States alone, the Centers for Disease Control & Prevention (CDC) estimates that 1 in 6 Americans become ill due to foodborne diseases, resulting in 128,000 hospitalizations and 3,000 deaths annually.
The most frequent causes of foodborne illness include bacterial contamination, such as E. coli and salmonella, and chemical contamination, like lead and other heavy metals. The traditional methods of detecting these contaminants (visual inspections and microbial testing) are time-consuming and error-prone. However, equipping a machine vision system can help solve these problems while analyzing images of food products and detecting contaminants. In this article, we will introduce the safety challenges in food production and how SmartMoreInside solves them with a set of advanced machine vision products.
Foreign Objects: Accidental contamination of food with foreign objects, such as glass, metal, or plastic, can pose serious health risks to consumers. Unfortunately, these objects can cause physical injury, choking, or even internal bleeding.
Deterioration: Food deterioration can occur due to improper handling, storage, or transportation in the food production facility. This can result in the growth of harmful bacteria, mold, or other pathogens, eventually leading to foodborne illnesses.
Missing Label: Incorrect or missing labeling on food products can lead to confusion among consumers, which may ultimately cause them to consume allergens or unintentionally violate their dietary or religious restrictions.
Expired Food: Consumption of expired food products can result in food poisoning or other illnesses and can equally cause serious health consequences.
No Tracking or Tracing: In the event of a foodborne illness outbreak, tracking and tracing the origin of the contaminated food products is essential to identify the source and prevent further contamination. Nevertheless, not all food producers have an effective tracking and tracing system like a machine vision system, and this ignorance can lead to delays in identifying the source of contamination and containing the outbreak.
Machine vision systems can play a crucial role in ensuring food safety by identifying and preventing contamination, defects, and other food processing and packaging issues. Accordingly, here are machine vision systems applied in food production that work together to protect food safety:
Before production begins, raw materials and ingredients must be stored properly to prevent contamination; barcode scanners track and identify materials, ensuring the correct ingredients are used in production. The barcode scanner reads the barcode on each material and sends the information to a database, which then tracks the material throughout the production process.
For example, a barcode scanner could track a bag of flour entering the production line, making sure that it is not contaminated and has not passed its expiration date. Not only that, but a barcode scanner of a machine vision system in a meat processing facility can likewise verify that the incoming meat is from an approved source and has been properly stored and transported.
During the production process, food products are inspected to ensure they meet quality and safety standards – industrial cameras, light sources, and industrial computers capture images of food products and analyze them for any defects or contaminants. The industrial camera captures high-resolution product images, which are then analyzed by the industrial computer, and the light source provides optimal lighting conditions for the camera to capture accurate images.
Let's consider an example; an industrial camera could be used to inspect a bag of fruit for any foreign objects, including but not limited to a tiny insect that could pose a safety risk to consumers. In extensive food production facilities, an industrial camera can be used to inspect signs of mold or other defects, while an industrial computer can be used to analyze the images and alert workers if any issues are detected.
Machine vision systems can also ensure food products are stored and delivered safely – barcode scanners can track the movement of food products throughout the supply chain, guaranteeing that they are stored at the correct temperature and delivered to the right location. Indeed, this can help prevent spoilage, contamination, and other issues arising during storage and delivery. That’s why food industries never hesitate to choose a reliable barcode scanner manufacturer for high-quality scanners.
For instance, a barcode scanner could track a box of packaged cookies moving from the production line to a storage area and then to a delivery truck for transportation to a retail store. Moreover, in a grocery store, a barcode scanner can track the movement of perishable products like dairy and meat, ensuring that they are stored at the correct temperature and sold before expiration.
Last but not least, here comes the protection of the complete process in food production, where SMore ViMo functions as a robust machine vision system solution developed by SmartMoreInside, a machine vision products manufacturer. Vision Inspection and More, or SMore ViMo for short, is an end-to-end intelligent industrial no-code platform that performs recognition, detection, segmentation, and classification for over a thousand industrial applications.
SMore ViMo offers various intelligent full-process services, such as data management, data labeling, model training, project design, model operation, and project administration. It has the potential to be used in a wide variety of industrial settings, including the detection of numerous objects, the identification of fractures, laser engraving, and the classification of bent characters.
Codes, whether barcode, QR code, or DPM code, have been widely adopted by industries for tracking and traceability, quality control, batch info recognition, and more. As applications become more complex, users demand agile and flexible code-reading capacity. With Smart Grid advanced capturing technology and advanced algorithms, SmartMore’s code-reading product and solution have enabled clients to speed up warehouse inbound and outbound logistics flows by 70% using batch scanning of up to 200 product units and integrating real-time data into IMS. SmartMore’s module can achieve full inspections for various types of supply chain management. Just follow SmartMore and start your advanced machine vision journey!