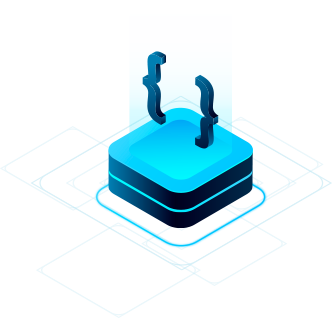
The SMore ViMo series products are equipped with intelligent production models for over 1000 segmented industry scenarios, embedded with over 50 tools such as algorithm enhancement, and can provide full stack intelligent capabilities for the entire manufacturing process of the industry. With the help of the SMore ViMo series of industrial products, a cross industry intelligent manufacturing ecosystem can be quickly built. SMore ViMo covers industrial intelligent clouds, deep learning training software, machine vision software, and other industrial products, providing data management, visual solution design, end-to-end running software, and other software to meet the visual needs of industry. The factory can quickly implement the entire process of model training, software integration, and production line deployment without the involvement of professional algorithm personnel, greatly reducing the threshold for the use of intelligent applications in the manufacturing industry and providing strong inclusive and intelligent capabilities for industry.
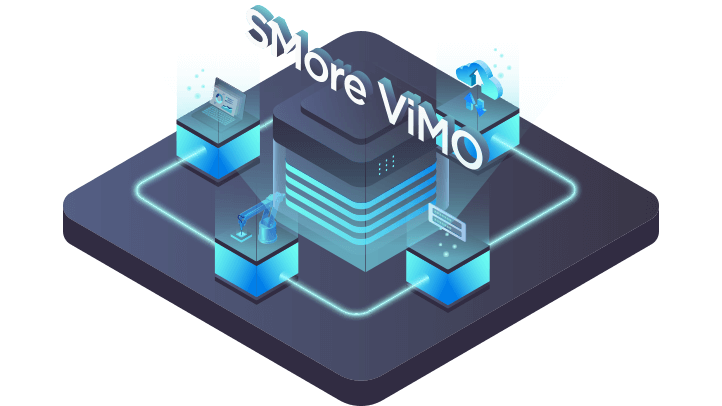
SMore ViMo provides data management, visual solution design, end-to-end running software, and more to meet the visual needs of the industry. The factory can quickly implement the entire process of model training, software integration, and production line deployment without the professional algorithm personnel, greatly reducing the threshold for the use of intelligent applications in the manufacturing industry and providing intelligent capabilities for industry. The Smore ViMo product matrix currently includes ViMo Cloud, ViMo Deeplearning, and ViMo Studio.